CASE STUDY:
Kannegiesser UK
About Kannegiesser UK
Sector: Industrial Machinery Manufacturing
Company size: 200-250
For this case study, we will explore Kannegiesser, a leading provider of advanced, automated laundry processing machinery for industrial, healthcare, and commercial laundry operations. Known for their adaptability and innovation, Kannegiesser has established itself as an expert in navigating and implementing rapid advancements in laundry technology. Their commitment to meeting the evolving demands of the industry positions them as a key player in delivering cutting-edge solutions for modern laundry processes.
Kannegiesser has an ongoing commitment to staying ahead of the competition through continuous improvements in production processes and product innovation. A key accomplishment in this area is the development of a custom SaaS tool designed to manage engineering change requests, specifically addressing product development and quality management needs. This system enables teams within the company to efficiently incorporate engineering feedback and make iterative product updates, driving advancements in innovation, product quality, and safety.
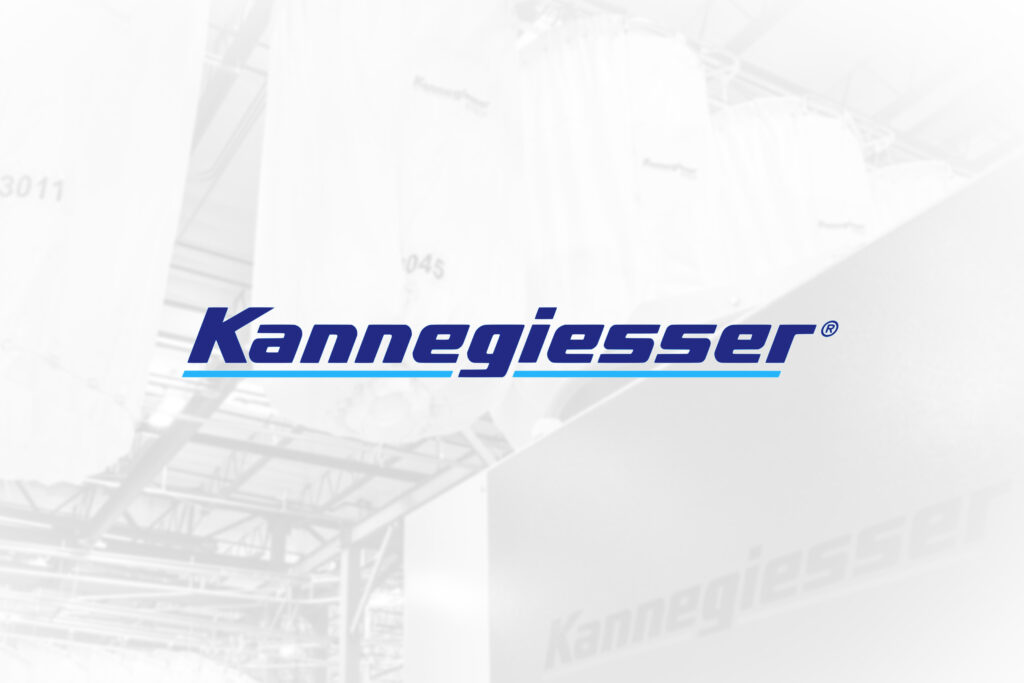
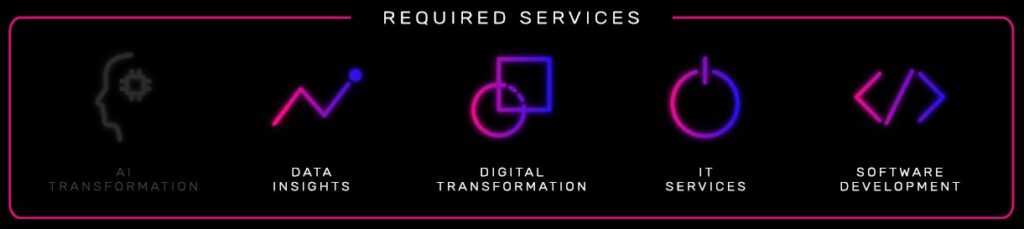
The Challenge
Kannegiesser sought to gain a competitive edge by increasing operational efficiency in their product design and management processes. A key obstacle was the lack of a formal assessment process for handling feedback from engineers, which often required coordination between multiple departments. This created inefficiencies and slowed down the product development cycle.
Their goal was to develop a solution that would streamline this process, providing a structured framework for future product improvements. The desired tool needed to automate workflow requirements for engineering change requests while ensuring compliance through a standardised approach.
The Solution
Through a collaborative partnership, we gained a deep understanding of Kannegiesser’s vision and values, enabling us to effectively support their mission to create a unique platform in the market. In August 2021, we began building the software from scratch, and by December 2021, version 1.0 was launched. This platform revolutionised Kannegiesser’s operational efficiency, leading to significant product innovations.
The previously labour-intensive process became automated, linking various departments directly to the workflow requirements. As a result, Kannegiesser was able to implement product design updates more rapidly, achieving savings in material procurement, enhancing product safety, and reducing production times.
Our partnership has fostered continuous evolution of the platform, which now includes additional features that deliver even greater benefits. The system has become fully integrated into Kannegiesser’s manufacturing process, with connections to other parts of the business. To ensure flexibility and security, we built the platform on a robust architecture hosted within our dedicated infrastructure, supporting constant changes and added functionality without compromising performance or long-term maintainability—crucial for meeting future demands.
Today, we remain directly involved in the ongoing development of the platform, using the Aspurian agile development approach to continuously introduce new functionalities that apply the latest innovations, creating lasting value for Kannegiesser.
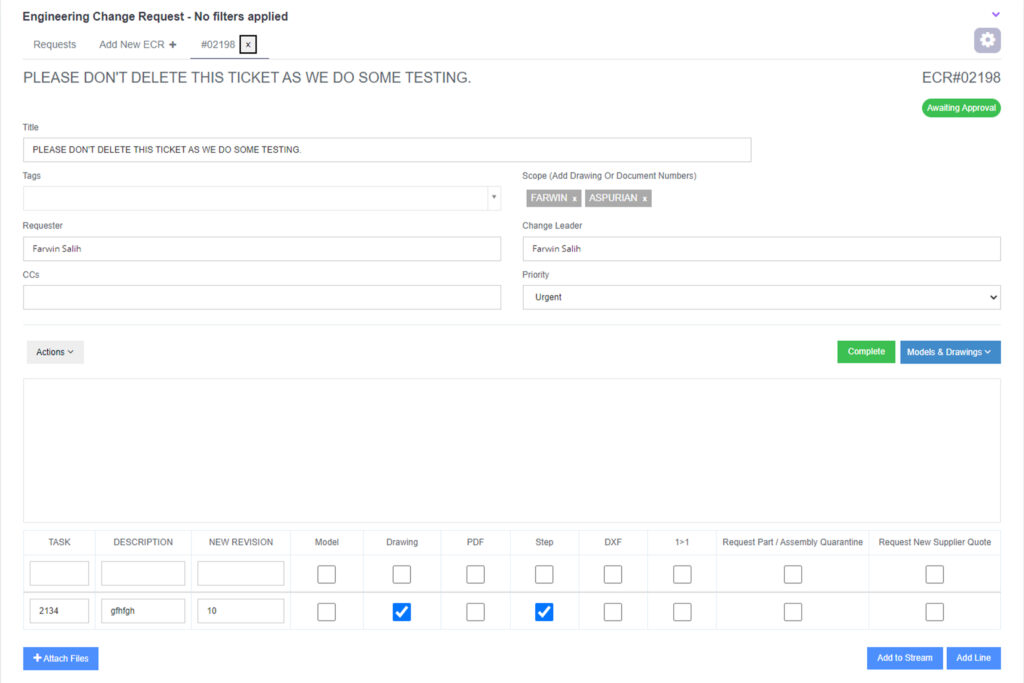
BENEFITS FROM THE SOLUTION
01
This platform revolutionised Kannegiesser’s operational efficiency, leading to significant product innovations.
02
Kannegiesser was able to implement product design updates more rapidly, achieving savings in material procurement, enhancing product safety, and reducing production times.
03
Our partnership has fostered continuous evolution of the platform, which now includes additional features that deliver even greater benefits.
04
We built the platform on a robust architecture hosted within our dedicated infrastructure, supporting constant changes and added functionality.